Aquajet compared to other tools
Cleaning method | Typical failure pattern paint failure upon…. | Number of required repairs in 5 years or 60 months | Side effects & issues |
Chipping, grinding | 3 to 4 months | => 15 to 20 repairs in 5 years | negative vetting & inspection, ship downgrading & rejection |
Hydrojetting | 8 to 24 months, subject to workmanship | => 2.5 to 7.5 repairs in 5 years | considerable accident risk, 10 t water/day, frequent breakdown |
Aquajet Blasting | 4 to 8 years | => 0.625 to 1.25 repairs in 5 years | training and crew supervision recommended |
High cleaning standard and watershield prevents: blast dust and explosion risk
Reasons why it is used on gas ships, in refineries, flammable areas and "no blast zones".
Plus: garnet as a natural stone => harmless to workers, nature and aquatic life.
Advantages of AQUAJET AJ-150 (big brother of AJ-50) versus high pressure water jet:
1) LOW AIR VOLUME
Needs only 200 cfm air flow.
2) LOW OPERATIONAL PRESSURE
Aquajet operates at very low pressures of 7-8 bar. All its components and hoses
operate below design limits therefore not easy breakable (pls note that a 500-
1000 bar water pump operates at design limits, and extremely high pressure
leads to frequent equipment failure and downtime: 50 % downtime is usual for
hydrojets)
3) NO RISK OF ACCIDENT
High pressure is the reason for hydrojetting equipment being known to be highly
dangerous. Water jets have caused numerous leg amputations!
4) NO NEED OF SPECIAL TRAINING:
Hydrojet workers need special training, special safety gear and/or certificates to
be allowed to work with 500-2000 bar.
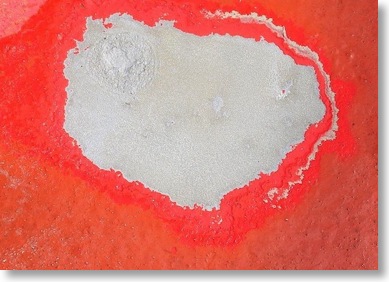
5) FEATHERING OF PAINT IN RUST SPOTS
This kind of "feathering" is of highest importance for lasting overpaint performance to avoid rust, water, salt crystals hidden under old paint protrusions.
Even 35,000 psi UHP cannot achieve feathering - it is impossible for water jetting.
Roughness Hydojetting cannot create the important "grip" or roughness profile of 20-30 microns needed for paint to adhere on steel and old paint. Garnet blasting creates this roughness even at a relatively low pressure.
6) HARD TO REACH AREAS
You can bend and direct Aquajet nozzles just as easy as a garden hose.
Perfect for work under and between pipes/structures.
Impossible for all hydrojets
7) LOW WATER CONSUMPTION
Aquajet water consumption is about 5 times lower than hydrojetting
Aquajet AJ-150 needs 7-8 bar air pressure, 200 psi air volume capacity and 1-
2 tons fresh water per day. A 500 bar water jet needs about 30 litres fresh water
per minute, usually 8-10 tons in 10 hours.
8) COST OF EQUIPMENT
Aquajet's price is a fraction of the cost of a 500 or 2000 bar water jet (which goes
from 15-30,000 to 70,000 USD)
Pressure Tool Comparison
1: If you connect a conventional 300 lbs shipyard blast set to the ship air onboard, nothing happens since ship air pressure is insufficient.
2: With a 390 cfm compressor, the conventional 300 lbs blaster blows out 50 to 80 kgs copper slag or sand per m2. (copper slag damages aquatic environment, correct procedure is to collect and return to shore. Sand harms your workers' lungs)
If crew is blasting just 8 days per month: | ||
A conventional blaster takes at least 60 kgs per m2, 40 m2/day | => 2.4 tons grit a day at 40 m2/day | => 19.2 tons per month (8 full blast days per month) |
Aquajet needs: 15-30 kgs p. m2, garnet is used 2-4 times, 40 m2/day | => 150 to 600 kgs garnet a day (=600/4 to 1200/2) | => 1.2 - 4.8 tons per month (8 full blast days per month) |
In comparison, a 500 bar hydrojet uses 10 tons fresh water per day | => 10 tons fresh water per day | => 80 tons per month . (8 blast days). Hydrojet breakdown far higher: hydrojets operate at design limits. |
Masters don't want to spend 80 tons water per month and don't like 20 tons of sand onboard: Aquajet is a wet abrasive blaster designed for low air conditions onboard, able to recycle used garnet with a grit consumption of 4 to 15 kgs/m2 (using garnet 2-4 times) instead of 50-80 kgs/m2 !.